The Next Era of Manufacturing
The Next Era of Manufacturing
Discover the emerging trends shaping the future of the Manufacturing industry. In this series, we delve into why these trends are crucial for the survival and success of Manufacturing companies and explore how your company culture and performance can be the key to thriving through these transformations. Join us every week for fresh insights and stay ahead of the curve.
Mark your calendars! On Wednesday, August 7 at 11:00 AM ET, we will host a webinar to expand on the topics explored in our research. Don’t miss this opportunity to gain deeper insights and engage with industry experts.
Save the date for our upcoming Global Forum, which will be held virtually on October 16-17! More details coming soon.
Denison Consulting Shows How Thriving Cultures Deliver 38% Higher Profit in Manufacturing
For our new industry spotlight series, we are harvesting insights from applying the Denison Model to selected industries to uncover the secrets of how successful cultures deliver maximum operating performance.
Denison Consulting knows that a strong company culture drives financial success in every industry and sector. Based on our 25 years of experience working with over 8000 clients and 5 million employee participants around the world, we have a vast amount of data, analytics, and expertise that provide actionable insights into creating cultures that deliver lasting performance success.
Recognizing the strategic value of culture – which in our definition encompasses the impact of leadership and organizational effectiveness – is just the first step for CEOs and other senior executives. The critical next step is to link these directly to operational and financial performance; however, this is where most culture initiatives break down – they are launched with limited operational rigor and generally low expectations for improving performance. However, we have seen the direct linkage between culture and performance over and over again.
This plays out across all industries. As shown in the graphic below, the companies with weaker cultures shown in the Denison Model results on the left had declining EBITDA and Revenue, whereas the thriving cultures saw significant performance improvement in both.
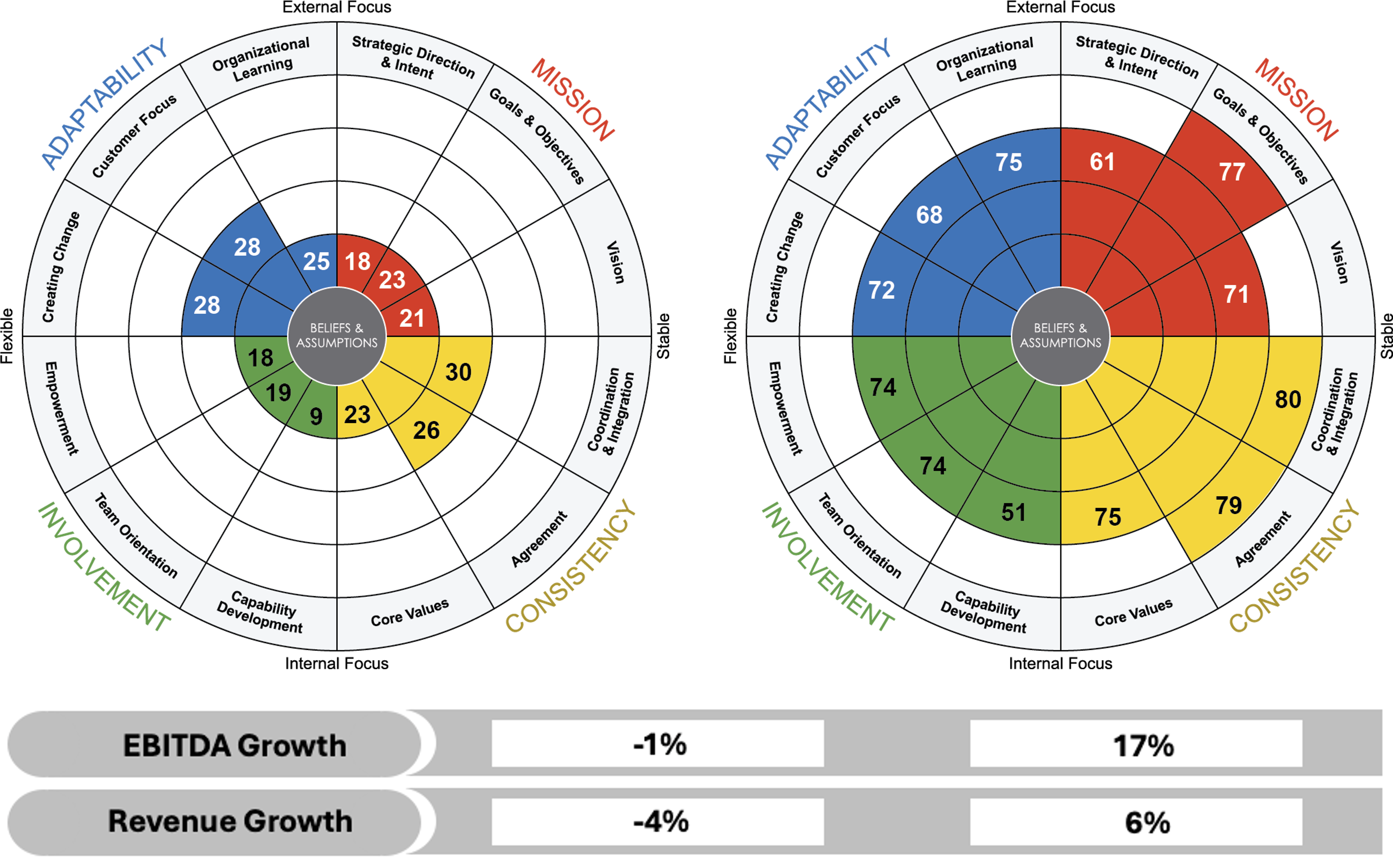
Specifically in the Manufacturing industry, our research highlights a striking 38% profit gap between Manufacturing companies with strong cultures and those with weak ones.
In our first industry spotlight, The Next Era of Manufacturing, we will share our insights from applying the Denison Model, our proprietary data, and advanced analytics to the Manufacturing industry to uncover traits of top cultures that drive profitability and operational performance.
Denison’s Global Benchmarking database shows that every successful culture in the Manufacturing industry requires Strategic Clarity, Team Orientation, and Empowerment. Employees who are clear on the direction of the company and how they fit into the company’s success, who are part of an effective team, and who are empowered to own their working outcomes produce a much stronger culture, are more productive, and generate higher levels of performance.
Yet, there is a critical gap in these areas between top and bottom-quartile companies. Manufacturing companies in the Top 25% score an average of over 80 on the Denison Model in Strategic Clarity, Team Orientation, and Empowerment, while companies in the bottom 25% score an average of under 15 points – a gap of over 70 points on each.
The good news is that lower-scoring cultures can learn from the top-quartile performers to lay out a roadmap for success. While there is no magic wand for improving Strategic Clarity, Team Orientation, and Empowerment, Denison has seen significant progress in these areas with the following actions:
- Executive Leadership Setting and Communicating Clear Direction and Engaging Directly with Plant Workers, Fostering a Sense of Alignment, Importance, and Empowerment
- Hiring and Developing Plant and Product Line Leaders that Embrace the Linkage Between Performance and Collaboration, Empowerment, and Coordination Across Functions
- Establishing Organization and Management Systems (i.e., organization structures, KPIs, goals/objectives, and processes) that Drive Team Orientation with Clear Linkage to Performance Success
Throughout our series, The Next Era of Manufacturing, we explore and highlight key insights from experience and expertise that show how effective cultures drive performance success in Manufacturing companies. Our topics will include:
Labor Shortage: Leveraging Culture in Your Talent Strategy to Improve Operations
Did you know that once hired, nearly a third of new employees leave within their first year if the company lacks a strong culture? We address the critical gap in skilled labor and strategies to attract and retain talent.
Culture Decline: A Leading Indicator of Rising Costs of Quality
Manufacturing companies with weak cultures incur scrap and rework costs about three times higher than those with strong cultures. We discuss the primary cultural factors that drive the cost of quality in most Manufacturing companies.
Optimizing the Cost of Safety and Performance
We explore the financial and human impact of safety measures and how to optimize them. We’ve seen that facilities with weak cultures experience five times as many LTA cases and six times as many recordable cases compared to facilities with strong cultures.
Culture, Digital Transformation, and the Future of the Manufacturing Process
We found that failing to integrate digital transformation strategies with human capabilities creates risks like increased operational errors, resistance to change, and underutilization of new technologies, representing sunk costs in your transformation investment. We outline ways to engage employees in your digital transformation efforts to create the intended performance success.
Leadership That is Both Performance and Culture Competent
Performance is non-negotiable, and leaders who are culture-competent plus operationally proficient are differentiators for their company’s success. Our analysis shows that one of the most potent competency combinations of leaders is Visionary Thinker + Open Communicator. These leaders have much more productive teams with stronger cultures.
Strategic Risks from Historical Blind Spots
Our analysis shows that ensuring people make the connection between the strategy and their performance goals and objectives is often assumed to have occurred. This adds risk to the strategy’s success. We outline ways to minimize this blind spot and risk.
The Next Era of Manufacturing is about harnessing the operational benefits of culture.
In this era, leaders in the Manufacturing industry will cultivate success by connecting cultural, organizational, and leadership insights to operational performance trends. Our goal with this research is to provide you with the tools and insights needed to transform your company. Together, we can navigate the complexities of the Manufacturing industry and create success.
Follow Denison Consulting for notifications of our Next Era of Manufacturing series and subscribe to our newsletter for updates as new analysis is released.
More about Denison Consulting.
By integrating culture with operating performance, we enable leaders and organizations to deliver lasting performance success. At Denison Consulting, we go well beyond the engagement and satisfaction of your workforce. We believe successful cultures should be measured by successful performance. That’s why we created the Denison Model.
8,000 clients globally. 5 million survey participants. 25 years of experience and expertise. Advanced analytics and AI. Actionable insights that deliver improved performance.
That’s Denison Consulting.
Contact us, and let’s discuss your performance journey.
A Thriving Culture is the Best Weapon Against Labor Shortages in Manufacturing
Labor shortages have long been a challenge in manufacturing, worsened by the COVID-19 pandemic and tight labor markets in recent years. The aging workforce and lack of young talent introduce more business risk for productivity, innovation, and growth. Simultaneously, global competition continues to intensify, further stressing labor markets in the US and abroad.
Manufacturers failing to secure and retain skilled workers will fall behind in this evolving landscape.
Today, 75% of manufacturing executives identify attracting and retaining quality talent as their primary challenge.1National Association of Manufacturers (NAM). “Attracting and Retaining a Quality Workforce.” NAM Survey. At Denison, we have seen that manufacturing companies with weaker cultures experience a turnover rate of nearly twice that of companies with higher-performing cultures – 32% for weaker cultures versus 15% for higher-performing cultures. These higher attrition rates for weaker cultures result in higher costs, lower productivity, and a more disconnected workforce.
Competing for and Retaining a Talented Workforce
Younger workers now prioritize company culture on par with salary and benefits2City Personnel. (2023). Company Culture Vs. Salary: What Matters Most To Job Seekers? Retrieved from https://citypersonnel.net/company-culture-versus-salary/, and this trend is growing across labor markets.3Employ Inc. (2022). Job Seeker Nation Report. Retrieved from https://web.jobvite.com/rs/328-BQS-080/images/2022-12-2022JobSeekerNationReport.pdf This shift increases the impact of company culture on job offer acceptance rates4Employ Inc. (2022). Job Seeker Nation Report. Retrieved from https://web.jobvite.com/rs/328-BQS-080/images/2022-12-2022JobSeekerNationReport.pdf and attrition, meaning a weak culture filters out top talent at every hiring stage and causes a productivity drain as experienced workers leave and are replaced with new hires.
Sadly, once hired, nearly a third of new employees leave within their first year if the company lacks a strong culture.5Richards, J. (2020). Do you have a turnover problem? Plant Services. Retrieved from https://www.plantservices.com/workforce/workforce-development/article/11291902/do-you-have-a-turnover-problem As we noted in our prior article about how thriving cultures deliver 38% higher profits in Manufacturing companies, employees must understand and believe their work is connected to the company’s strategic success for the culture to support the retention of skilled workers.
When failure to attract couples with inability to retain, hiring and onboarding costs skyrocket, eroding profit margins. Over time, this leads to a stagnant, demotivated workforce, resulting in lower quality, increased safety incidents, and further financial losses as your business performance declines at an accelerated rate.
Identifying Root Causes
As we’ve worked with manufacturing clients over the last 25 years, we’ve seen a focus on these key drivers improve recruitment and retention:
- Strategic Alignment: Clear strategic direction and alignment of goals and objectives throughout the organization – from the CEO to the shopfloor – has been proven to boost employee motivation, productivity, and retention. This environment also results in becoming a “destination employer” – providing the company the ability to hire the best talent.
- Business Environment Consistency: Stability and predictability in daily operations reduce stress and turnover. This is facilitated by consistent and effective organization, leadership, and management system effectiveness.
- Innovation and Learning: Continuous improvement and learning opportunities keep employees engaged and loyal. Combined with strong Strategic Alignment and Business Environment Consistency, these serve as foundations for creativity, encouraging and equipping the workforce to continuously improve the way work is done.
- Flexibility: Even non-telework roles expect flexibility today, such as compressed work weeks, shift swapping, and flexible hours. Flexibility, within reason, has the opposite effect of what most employers worry about – it actually improves productivity.
From Deficit to Dominance
The Denison Model goes beyond industry best practices, leveraging deep analytics, to connect your business performance metrics to measures of your culture, so you can assess positive and negative factors across groups and pinpoint actionable priority areas.
In the case example below, you can see the retention rate differences between production and office locations.
While core values contribute to attrition in both cases, the production sites surfaced concerns about unethical behavior and uncooperative teams as drivers of attrition. This root cause detail would be lost in most surveys’ blended average feedback. The Denison Model highlights and clarifies these priority areas that will maximize return on investment in recruitment and retention.
In this example, you also see that the production group with stronger retention rates, 78 versus 48, in 2023 faces similar short-term cultural challenges, suggesting it is at risk of higher turnover problems in 2024. With this information, leadership can take immediate corrective action to prevent further decline.
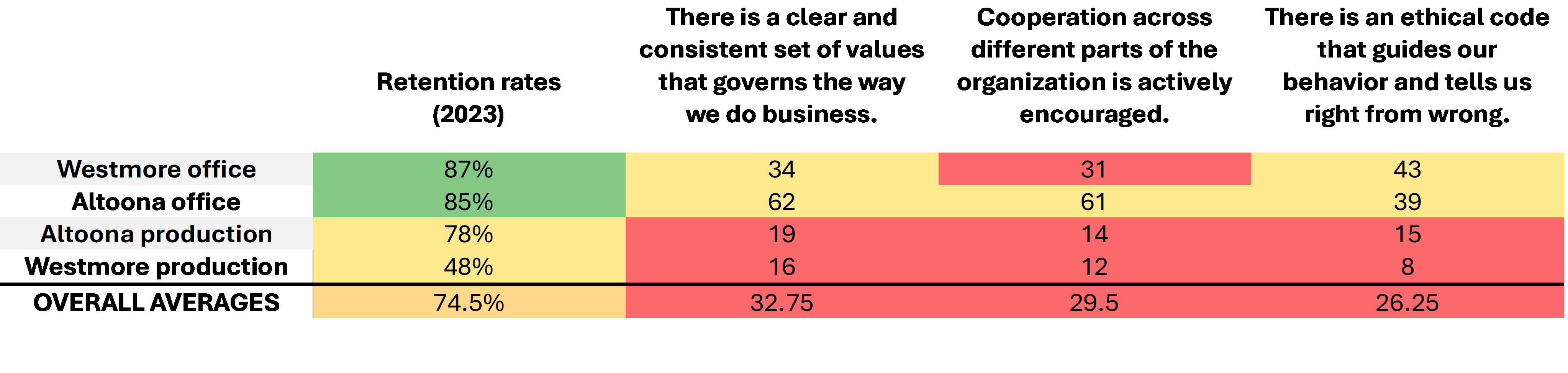
Our experience repeatedly shows that linking your unique cultural attributes to crucial business performance outcomes, like retention, creates a robust action plan that directly enhances financial performance. Used over time, the Denison Model empowers you to correct issues and proactively manage the evolution of your culture to accelerate business performance.